Costes Indirectos de Fabricación
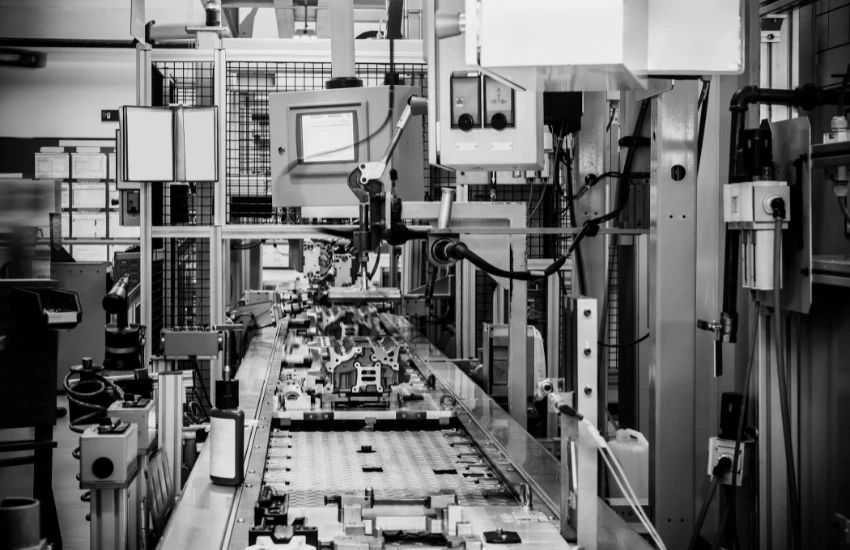
Un aspecto fundamental en el Control de Gestión es la correcta determinación de los costes del producto. A priori, basándome en mi experiencia, se aplican casi tantos métodos de cálculo como empresas y criterios puedan existir.
Algunos métodos de determinación son básicamente una bomba de relojería, en el caso de que sean usados como base para la toma de decisiones. Otros, aquellos que son más o menos acertados. Y, por último, los que sencillamente no alcanzan su objetivo ni se les suponen más pretensiones formando parte de ese grupo del “aquí siempre se ha hecho así”.
El Coste de Producción
La resolución de 14 de abril de 2005 del Instituto de Contabilidad y Auditoría de Cuentas (ICAC) por la que se establecen los criterios para la determinación del coste de producción expresan que, el coste de producción incluirá el precio de adquisición de las materias primas y otras materias consumibles, el de los factores de producción directamente imputables y la fracción que razonablemente corresponda de los costes de producción relacionados con el activo en la medida en que (…) se basen en el nivel de utilización de la capacidad normal de trabajo de los medios de producción (…).
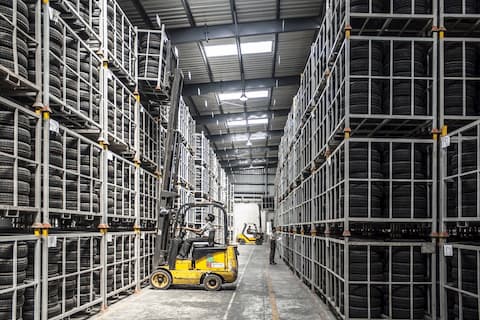
Más adelante, habla sobre los “rasgos y características que delimitan el modelo para determinar el coste (…): El coste se cuantifica a partir de un modelo de costes reales completos incurridos durante la fabricación, elaboración o construcción del producto; el reparto de los costes indirectos de producción se debe realizar según el nivel de utilización de la capacidad normal de producción de la empresa, y, no se incluyen los costes de inactividad o subactividad”.
Siempre será recomendable aplicar, además del criterio de puesta en almacén, los costes adicionales que se produzcan hasta que dichos bienes se encuentren en el almacén tales como transportes, seguros y aduanas.
El mencionado criterio de puesta en almacén es aquel, a través del cual, se valorará la entrada de los materiales en el almacén según el precio de compra en factura.
Siguiendo el criterio propuesto, los costes directos más comunes son los materiales, ya que pueden ser asignados al producto de forma inmediata.
Entre ellos tenemos:
Coste de Mano de Obra
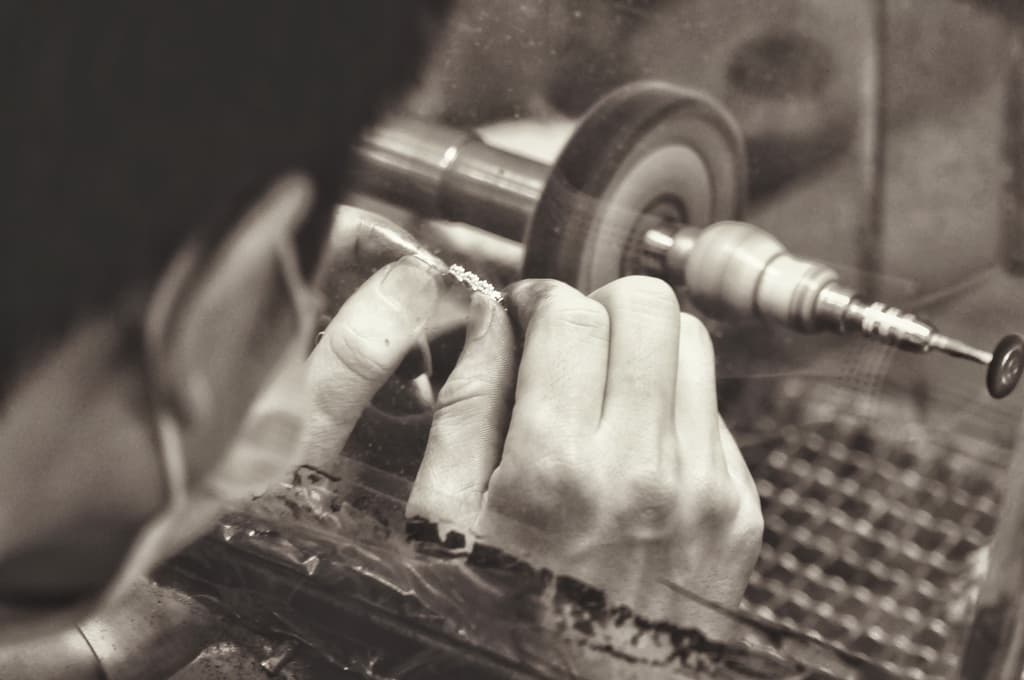
El coste de mano de obra puede tener un componente directo (costes que se asignan de forma inequívoca al producto) o indirecto (no pueden asignarse de forma inequívoca al objeto de coste tratado). Por ejemplo, el personal encargado del mantenimiento de los equipos de fabricación.
De forma sencilla, la empresa puede calcular el coste/hora de la mano de obra directa estableciendo la relación entre su Coste total y el número de horas realmente productivas (sin tener en cuenta ausencias remuneradas, vacaciones, tiempos muertos, etc.). El tiempo productivo no debe coincidir necesariamente con el tiempo contratado.
Los Costes Indirectos de Fabricación
Los costes indirectos de fabricación, los cuales y según el ICAC se corresponden a aquellos “que se derivan de los recursos que se consumen en la fabricación, elaboración o construcción de un producto, afectando a un conjunto de actividades o procesos que no resulta viable una medición directa en la cantidad consumida por cada unidad de producto. Por ello, para su imputación al producto, es necesario emplear unos criterios previamente definidos”.
Los costes indirectos de fabricación que se corresponden a este criterio son múltiples y muy variados, pero podemos destacar fundamentalmente:
La Mano de Obra Indirecta
La mano de obra indirecta que, como se indica, recoge costes no asignables directamente al producto.
Costes Derivados del Uso del Activo no Corriente
Son todos aquellos gastos relacionados con insumos que se deprecian en el proceso productivo, así como todos aquellos gastos relacionados con su mantenimiento y reparaciones necesarias por el uso.
También se engloban dentro de estos costes todos aquellos materiales y repuestos consumidos en dicho proceso de mantenimiento.
Costes Procedentes de Servicios Exteriores
Engloban al conjunto de servicios exteriores tales como arrendamientos, servicios profesionales, transportes, primas de seguros, suministros, etc., que pueden imputados de manera indirecta al objeto de coste sujeto a análisis.
Más acerca de los Costes Indirectos
Es muy importante tener en cuenta que los costes indirectos están más relacionados con la capacidad productiva máxima de producción que puede alcanzar la empresa que con la producción real.
Es decir, la amortización de los equipos productivos existentes, el pago del alquiler de la nave destinada a la fabricación, el mantenimiento de los almacenes, las primas de seguros pagadas, etc…, en general, serían los mismos a plena capacidad y no varían en función de la producción.
Tal y como exponen Hrongren, Datar y Foster en su trabajo Contabilidad de Costes: Un enfoque gerencial, es en este punto donde corremos el riesgo de ser víctimas de la denominada espiral de la muerte o espiral decreciente de la demanda sobre la que profundizaremos en un futuro artículo. Además esto es el resultado de una política de disminución de la producción para reducir costes, aplicando al producto los costes fijos correspondientes al exceso de la capacidad productiva.
Lo anterior implica que, si nuestro sistema de cálculo de costes incorpora todos los costes indirectos, la decisión de determinar el nivel de capacidad de producción sobre el que basar el cálculo del coste indirecto por unidad se convierte en una importante decisión empresarial.
Una Consideración sobre la Estimación del Coste Indirecto
Desde el área de Finanzas y Control de Gestión de Altair, recomendamos siempre estimar el coste indirecto por unidad, en la capacidad normal basada en el análisis de un periodo histórico de, entre dos y cuatro años, en función del periodo de madurez en el que se encuentre la empresa, considerando como coste de subactividad en el coste del periodo a aquellos costes fijos para el caso de que la capacidad real quede por debajo de la normal.
Ejemplo de Cálculo de Coste Unitario
Se ha estimado que la capacidad de producción normal es de 10.000 unidades, pero finalmente se han producido 8.000 unidades.
Normal | Real sin Subactividad | Subactividad como Gastos del Periodo | |
Capacidad de Producción (Ud) | 10.000,00 | 8.000,00 | 8.000,00 |
Costes Fijos (€) | 6.300,00 | 6.300,00 | 5.040,00 |
Subactividad (€) | 1.260,00 | ||
Coste Unitario (€/ud) | 0,63 | 0,79 | 0,63 |
En este caso en que la producción real sea menor, si calculamos el coste unitario en base al total de los gastos fijos (Real sin Subactividad) se estará penalizando al producto con un coste unitario mayor (0,79 €/Ud.) ya que la menor fabricación deberá absorber la totalidad de los costes fijos de fabricación.
Teniendo en cuenta la presencia de unos costes de subactividad y una vez calculado el coste fijo unitario para la capacidad normal, calcularemos los costes fijos asignados al producto para la capacidad normal (0,63 €/Ud. x 8000 unidades). La diferencia, entre los 6.300 € (costes fijos de producción) y los 5.040 € (costes fijos de producción imputables al producto) formarán parte de la subactividad como gasto del periodo.
De este modo, el coste unitario permanecerá fijo ante una bajada de la actividad.
Esperemos que este Post haya resultado de tu interés.
¿Necesitas más información al respecto?
Contacta con nosotros y un experto te asesorará y te ofrecerá, sin compromiso alguno, la forma de ayudarte a mejorar la gestión de tu empresa.
Javier Ruiz Bermúdez
DIRECTOR DE ÁREA
Finanzas y Control de Gestión